Comparative Analysis of Nickel-Based Alloys and Other Alloy Materials
Nickel-Based Alloys: Overview
Nickel-based alloys primarily consist of nickel as the base metal, with other elements like chromium, molybdenum, iron, and cobalt added to enhance specific properties. These alloys are known for their excellent high-temperature strength, resistance to oxidation and corrosion, and good mechanical properties. They are particularly favored in environments with extreme temperatures and aggressive chemicals.
Key Characteristics:
High-temperature performance: Nickel-based alloys can withstand temperatures exceeding 1000°C, making them ideal for applications such as turbine blades in jet engines and nuclear reactors.Corrosion resistance: The addition of chromium and other elements gives these alloys outstanding resistance to oxidation, pitting, and stress corrosion cracking.
Strength and durability: These alloys retain their mechanical properties even under extreme stress and at high temperatures.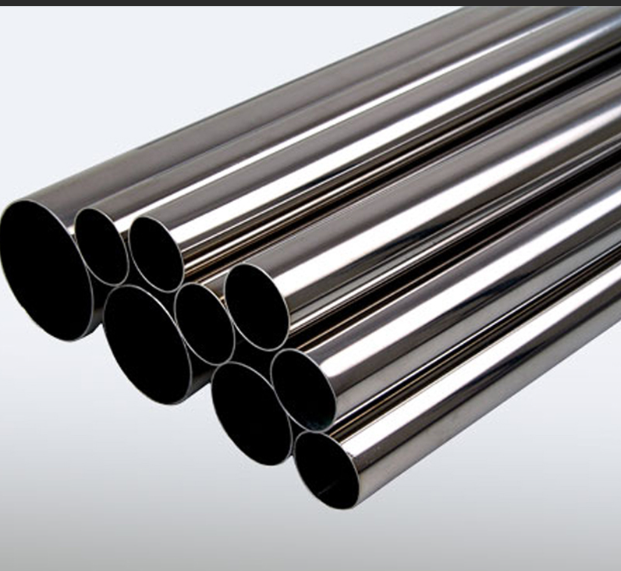
Comparison with Other Alloys
1. Iron-Based Alloys (Steel)
Iron-based alloys, such as carbon steel, stainless steel, and tool steel, are widely used across various industries. Steel is favored for its strength, cost-effectiveness, and versatility. However, when compared to nickel-based alloys, iron alloys have limitations in high-temperature performance and corrosion resistance.
Key Differences:
- Temperature Resistance: While steel can withstand moderately high temperatures, it tends to lose its strength at temperatures above 500°C. Nickel-based alloys, in contrast, maintain their strength and stability at much higher temperatures.
- Corrosion Resistance: Stainless steel offers some corrosion resistance due to its chromium content, but nickel alloys outperform steel in highly corrosive environments, such as in marine applications or in chemical processing.
- Cost: Steel is significantly less expensive than nickel-based alloys, making it the material of choice for many low-cost applications. However, for critical high-performance environments, nickel alloys justify their higher cost due to their superior properties.
2. Titanium Alloys
Titanium alloys, composed mainly of titanium with small amounts of aluminum, vanadium, and other elements, are known for their exceptional strength-to-weight ratio, high corrosion resistance, and biocompatibility. They are commonly used in aerospace, medical implants, and marine applications.
Key Differences:
- Strength-to-Weight Ratio: Titanium alloys excel in applications requiring lightweight yet strong materials, such as in aerospace and sports equipment. Nickel alloys, while strong, are denser and thus may not be the best choice for weight-sensitive applications.
- Temperature Resistance: While titanium alloys perform well at temperatures up to about 600°C, nickel-based alloys offer superior high-temperature performance, making them more suitable for high-heat applications like jet engines and gas turbines.
- Corrosion Resistance: Both titanium and nickel alloys provide excellent corrosion resistance. However, nickel-based alloys have an edge in extreme environments like high-temperature chemical processes, where titanium may not perform as well.
3. Aluminum Alloys
Aluminum alloys are lightweight, have good corrosion resistance, and are widely used in automotive, aerospace, and packaging industries. They are available in various grades, from soft and malleable to hard and strong.
Key Differences:
- Weight: Aluminum alloys are much lighter than both nickel-based and titanium alloys. This makes them ideal for applications where reducing weight is a priority, such as in the automotive industry.
- Temperature Resistance: Aluminum alloys generally perform poorly at high temperatures compared to nickel-based alloys. They start to lose strength at temperatures above 150°C, whereas nickel alloys can withstand extreme temperatures well over 1000°C.
- Corrosion Resistance: While aluminum alloys resist corrosion due to the formation of a protective oxide layer, they are not as resistant to high-temperature oxidation or chemical corrosion as nickel-based alloys.
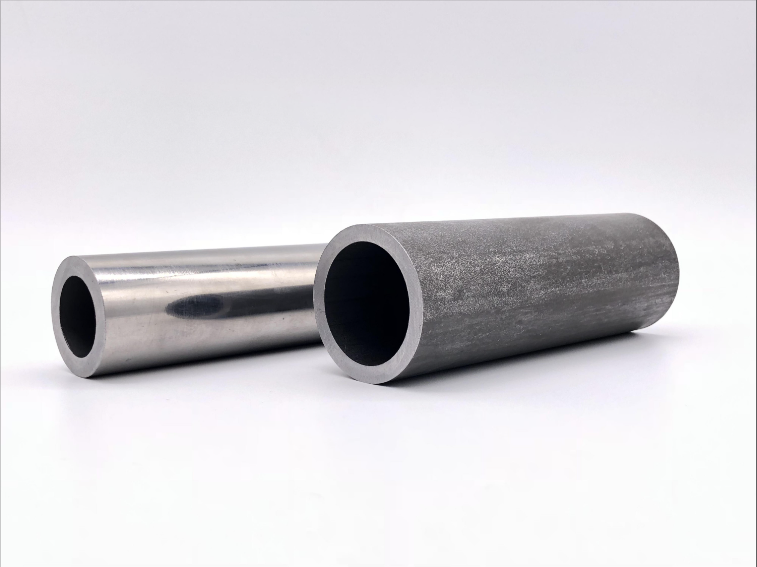
Applications of Nickel-Based Alloys
Due to their unique properties, nickel-based alloys are used in demanding applications such as:
- Aerospace: Turbine engines, heat exchangers, and exhaust systems.
- Power Generation: Gas turbines, nuclear reactors, and other high-temperature applications.
- Chemical Processing: Equipment used in aggressive chemical environments, such as reactors, heat exchangers, and distillation columns.
- Marine: Offshore oil platforms, ship engines, and components exposed to seawater.
Conclusion
Nickel-based alloys stand out in applications requiring high strength, resistance to high temperatures, and excellent corrosion resistance. While other alloys such as iron-based alloys, titanium alloys, and aluminum alloys offer advantages in certain areas, nickel alloys are often the preferred choice in extreme environments where performance is critical. The key takeaway is that the selection of an alloy depends on the specific needs of the application, considering factors such as temperature, weight, corrosion resistance, and cost.
In industries where performance is paramount, particularly in aerospace, power generation, and chemical processing, the properties of nickel-based alloys provide unmatched reliability and durability. Their high cost is often justified by the critical nature of these applications, ensuring the longevity and safety of critical components.
FAQs
What are high-temperature alloys made of?
Nickel, cobalt, or titanium are regularly used to craft high-temperature alloys. These metals can withstand highly high warmth without losing strength.
Why are high-temperature alloys used in jet engines?
Jet engines create severe warmth once they burn gas. High-temperature alloys are used because they may resist melting and remain robust under these conditions.
Can high-temperature alloys be utilized in spacecraft?
Yes, high-temperature alloys are essential in spacecraft. They are used for elements like high-temperature shields and rocket engines, which face extreme heat and are bloodless.