Key Properties of Nickel-Based Alloys
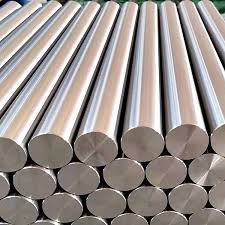
Nickel-based alloys are primarily composed of nickel, often combined with elements like chromium, cobalt, molybdenum, and iron. These alloys exhibit several standout properties:
- High-Temperature Strength: Nickel-based alloys maintain their mechanical integrity at temperatures exceeding 1,000°C, making them indispensable in high-heat environments.
- Oxidation and Corrosion Resistance: Chromium and other alloying elements form a protective oxide layer, enabling these alloys to resist oxidation and corrosion, even in aggressive environments like those containing acidic or saline substances.
- Creep Resistance: Under prolonged stress at high temperatures, nickel-based alloys exhibit remarkable resistance to creep, ensuring long-term stability.
- Versatility: Their adaptability to various fabrication methods, such as casting, forging, and additive manufacturing, makes them suitable for complex and precise applications.
Applications Across Industries
Nickel-based alloys are at the forefront of technological advancements in multiple industries:
- Aerospace: Turbine blades, engine components, and exhaust systems leverage the high-temperature capabilities of nickel-based alloys to ensure efficiency and reliability.
- Energy: In nuclear power plants, nickel alloys provide corrosion resistance and structural stability in reactors and steam generators. Gas turbines and solar energy systems also utilize these materials for their thermal properties.
- Chemical Processing: Equipment such as heat exchangers, reactors, and piping systems benefits from the corrosion resistance of nickel alloys, especially when handling aggressive chemicals.
- Marine Engineering: Nickel-based alloys are crucial in seawater desalination systems, offshore platforms, and shipbuilding, where they combat saltwater-induced corrosion.
Challenges and Advancements
Despite their exceptional qualities, nickel-based alloys face challenges such as high production costs and resource limitations. However, ongoing research is addressing these issues:
- Additive Manufacturing (AM): Advances in 3D printing technologies enable the creation of intricate nickel-alloy components, reducing material waste and production costs.
- Alloy Design Optimization: Computational modeling and artificial intelligence aid in developing new alloy compositions with tailored properties for specific applications.
- Sustainability: Efforts to recycle and reuse nickel-based alloys contribute to reducing environmental impact and resource consumption.
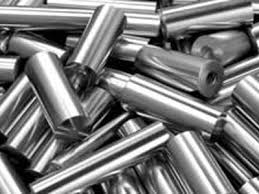
Future Perspectives
As industries demand higher performance from materials, nickel-based alloys are poised to remain at the forefront of innovation. Emerging technologies like hydrogen energy systems, advanced aerospace designs, and deep-sea exploration rely on these alloys to meet increasingly stringent requirements.
Conclusion
Nickel-based alloys stand out as indispensable materials in high-temperature and extreme environments. Their unparalleled combination of strength, resistance, and adaptability ensures their continued relevance in cutting-edge applications. As research and technology progress, these alloys will undoubtedly shape the future of engineering and industrial innovation.
FAQs
What are high-temperature alloys made of?
Nickel, cobalt, or titanium are regularly used to craft high-temperature alloys. These metals can withstand highly high warmth without losing strength.
Why are high-temperature alloys used in jet engines?
Jet engines create severe warmth once they burn gas. High-temperature alloys are used because they may resist melting and remain robust under these conditions.
Can high-temperature alloys be utilized in spacecraft?
Yes, high-temperature alloys are essential in spacecraft. They are used for elements like high-temperature shields and rocket engines, which face extreme heat and are bloodless.